Turnkey Dismantling, Modification, and Relocation of a Multi-Glove Isolator System for a Biopharma Manufacturer
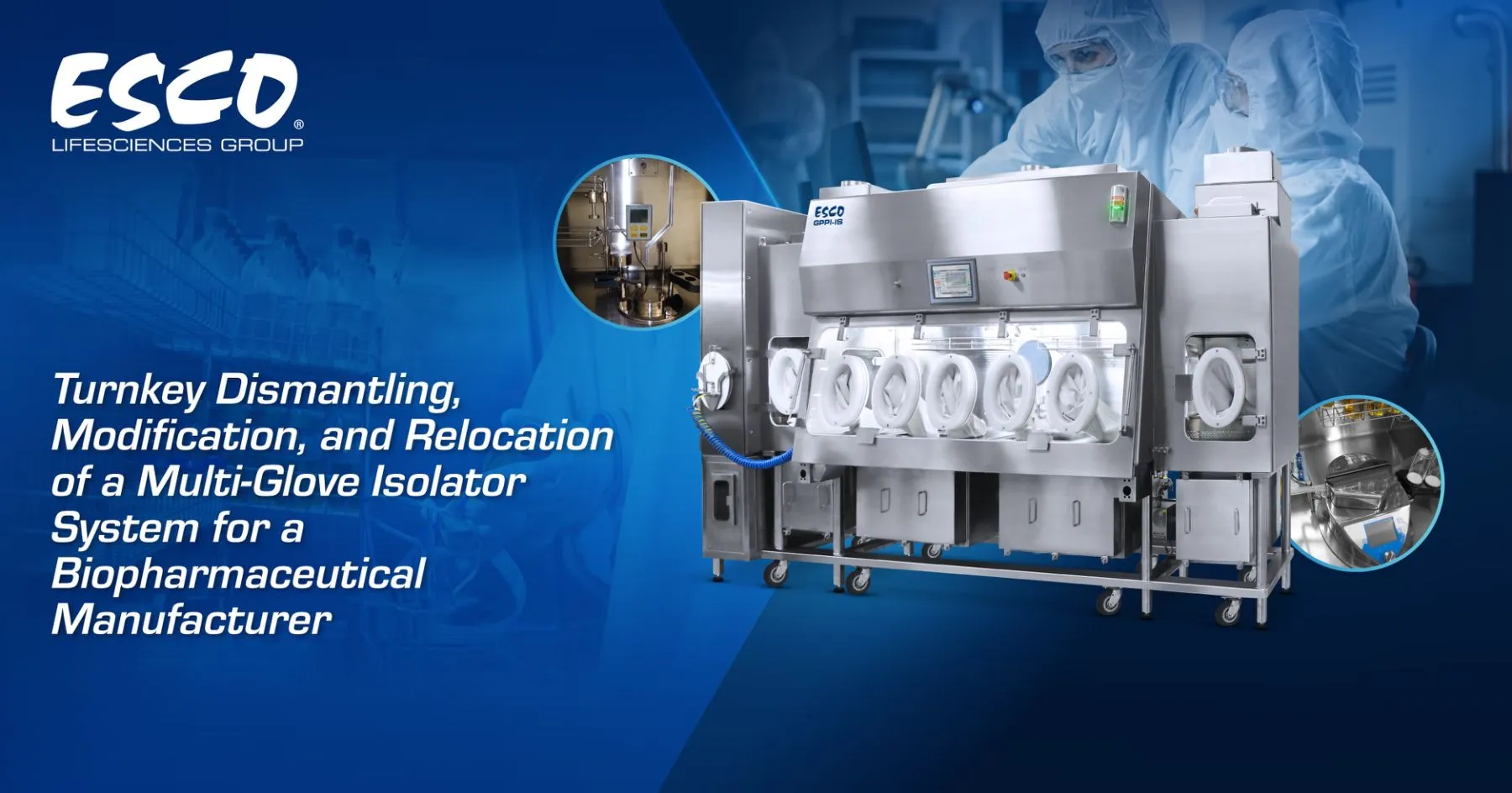
Case Study: Turnkey Dismantling, Modification, and
Relocation of a Multi-Glove Isolator System for a Biopharma Manufacturer
Client: Confidential
Industry: Biopharmaceutical Manufacturing
Project Locations: Northeastern United States, to Esco USA Facility in Pennsylvania,
to Gulf Coast of the United
States
Project Duration: 4 Months
Date: June 2025
Project Overview
A leading biopharmaceutical manufacturer
partnered with Esco team to manage the end-to-end dismantling, retrofit, and
relocation of a critical isolator unit. The project scope included equipment
disassembly, custom modifications, interstate logistics, and final installation
at a GMP production facility—requiring expert coordination and strict
compliance with regulatory standards.
Executed across three separate locations, this
complex, multi-stage operation was completed with zero disruption to ongoing
operations and full adherence to GMP protocols. Ultimately, the
client saved over 50% of the capital cost of a new sterility test isolator and
shortened lead time by 3 to 4 months. Furthermore, the isolator was delivered
with a new factory warranty.
Objectives
-
Safely dismantle and cleanly remove a 5-glove isolator system from a production site.
-
Retrofit the unit to support the latest sterility testing pump with footswitch integration.
-
Install custom 316 stainless steel racking and shelving in both the transfer and main chambers.
-
Professionally crate, transport, and reinstall the modified unit at a new biomanufacturing facility.
-
Re-commissioning and perform new Installation and Operation Qualification (IQ/OQ).
Project Execution Summary
-
Dismantling & Removal (Client Facility – Northeastern U.S.)
Esco technicians provided all labor and equipment necessary to safely dismantle and extract the isolator system. All activities were completed in accordance with site-specific safety procedures and contamination control protocols.
-
Packing, Crating & Transport (From Client Facility – Northeastern U.S. to Esco Facility – Pennsylvania)
Following disassembly, the unit was securely packed and crated for transport to the original equipment manufacturer (Esco) for factory-authorized modifications.
-
Technical Modifications (Esco Facility – Pennsylvania)
At the Esco facility, the isolator was modified to accommodate a modern sterility testing pump, complete with integrated footswitch control. Additionally, high-grade 316 stainless steel shelving systems were custom-fabricated and installed within the isolator's chambers to improve workflow and capacity.
-
Re-Crating & Delivery to Final Site (To Client’s New Facility – Gulf Coast U.S.)
The upgraded isolator was professionally re-crated and shipped to the client’s new production facility in the Gulf Coast region.
-
Final Delivery & Installation (Client’s New Facility – Gulf Coast U.S.)
Upon arrival, the Esco team managed unloading, internal relocation, placement, and final alignment of the unit according to the client’s designated production layout and specification.
-
Validation and Qualification
Following successful installation, the team fully recommissioned the equipment and delivered a new IQ/OQ document, enabling the client to proceed to PQ and production testing.
Challenges and Solutions
This project presented several critical
challenges that required precise planning, expert coordination, and innovative
solutions to ensure successful execution without disrupting operations. One of
the primary challenges was the cross-country transport of fragile, high-value
pharmaceutical equipment. To safeguard the isolator system during transit, the
Esco team designed and employed shock-absorbent crating, utilized real-time
shipment tracking, and leveraged specialized handling equipment, ensuring the
unit arrived at each location protected and on schedule.
Integrating legacy equipment with modern
production tools posed another significant hurdle. Our team worked closely with
the client’s engineering groups to ensure functional compatibility while
maintaining regulatory compliance throughout the process.
Finally, the project demanded strict adherence
to tight timelines and GMP standards across multiple sites. To meet these
requirements, the Esco team developed a detailed project execution plan
featuring built-in quality assurance and control checkpoints, along with
contingency measures—enabling seamless coordination and zero disruption.
Conclusion
Esco successfully delivered a
complex, multi-site equipment relocation while meeting strict regulatory and operational requirements. Through close coordination, expert
engineering, and GMP-focused execution, the team ensured a smooth transition
from dismantling to final qualification.
The client not only accelerated deployment
timelines by 3 to 4 months but also significantly reduced more than 50% capital
expenditure of sourcing a brand-new isolator system. With upgraded
functionality, full compliance, and a renewed factory warranty, the delivered
solution met all production and regulatory demands, with zero disruptions to
ongoing operations.
Esco’s end-to-end approach, combining custom
engineering, regulatory expertise, and coordinated execution, reinforced the
value of revitalizing existing assets to meet modern pharmaceutical standards
in a cost-effective, time-efficient manner.