Isoclean® Healthcare Platform Isolator - Without Filter Below Workzone
Optimized Solution for Aseptic/Hazardous Applications
The Isoclean® Healthcare Platform Isolator (HPI-G3) facilitates the isolation of a product or process while providing the required aseptic/hazardous environment. It is configured to operate at positive or negative pressure in recirculating airflow. This equipment provides a comprehensive range of personnel and product protection in addition to the surrounding work areas and the environment.
Inbuilt dampers to allow pressure testing without having to use cover plates, tape & silicone
Centrifugal, direct-drive blowers designed for maximum energy efficiency and minimal maintenance
Sentinel™ Gold Microprocessor Control System supervises all functions and monitors airflow and pressures in real-time
Airlock pass-through chamber ensures work zone remains sterile during insertion and removal of items
Horizontal sliding tray prevents operator fatigue during transfer procedures
Electromagnetic Interlocking Doors with time delay effect ensures safety and containment between the Pass Chamber and the Process Chamber
Optional sharps disposal system enables smoother work flow and minimizes transfers in order to enhance patient protection and sterility
HEPA filters (H14) with a typical efficiency of >99.995% at 0.1 to 0.3 microns provide superior ISO Class 3 air cleanliness, 100 times better than competing products
LED lamps deliver >650 Lux to the work surface for superior overall illumination
With ISO Class 3 environment, the Process Chamber facilitates aseptic processing in an EU GMP Grade A condition
Frameless front visor panel with highly rounded edges to minimize crevices and maximize door vision panel
Circular glove ports with minimal crevices, no exposed bolts and nuts
Single-piece stainless steel work surface with raised edges on all sides contain spillages
Optional adjustable hydraulic stand, with casters, elevates to accommodate user preference for sitting or standing work surface height
Angled drain pan for easy cleaning
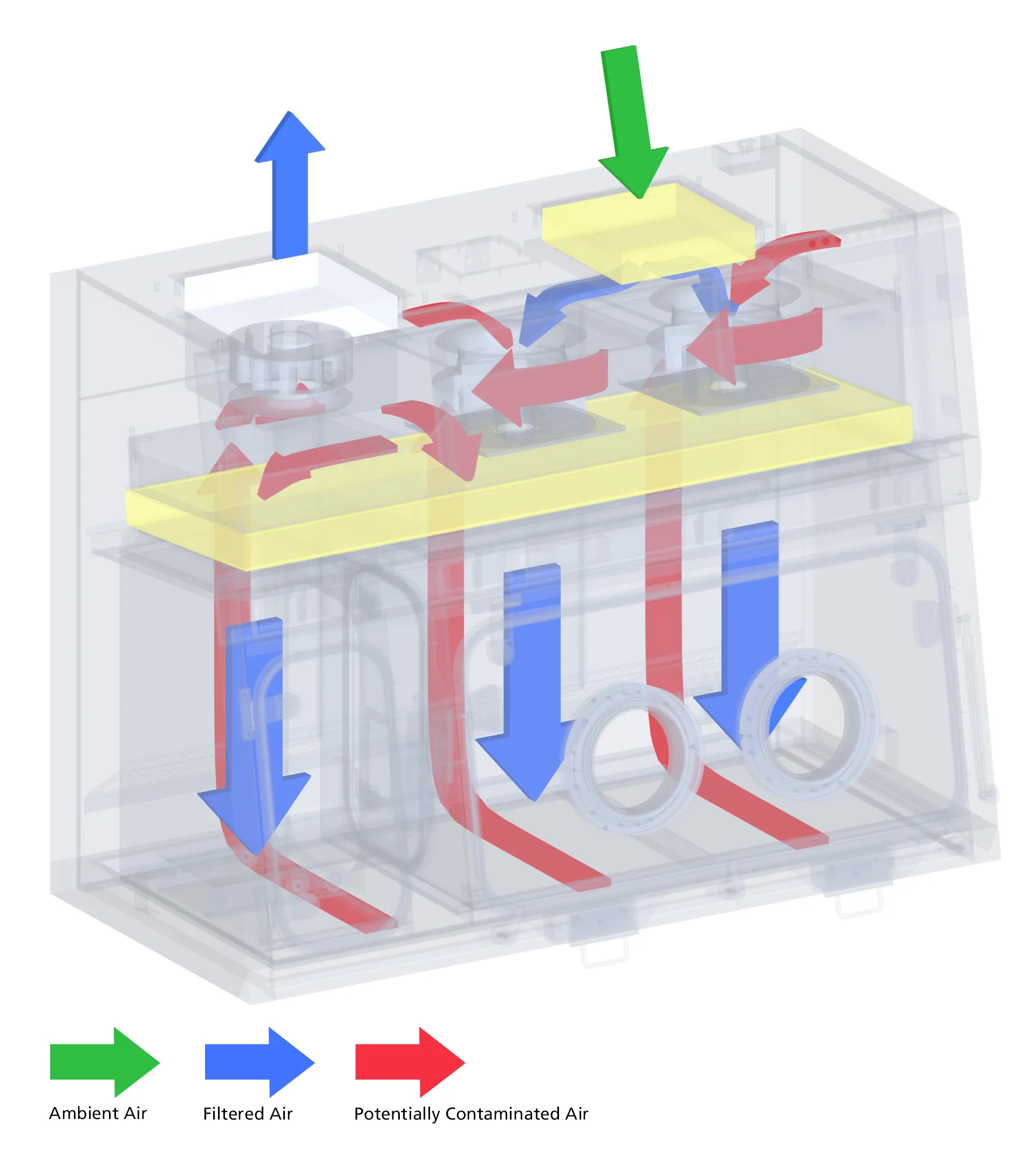
Ambient air is pulled through the inlet pre-filter located on top of the isolator. The pre-filter traps large size particles to extend the life of the supply HEPA (H14) filter.
Air from the top inlet and from work zone is pulled by the fan which creates a positive pressure on the plenum that creates downflow. In positive pressure model, the proprietary plenum design forces more air into the work zone, increasing its pressure relative to the pass-through. In negative pressure model, the work zone and pass-through interchange are under negative pressure to the room, thereby preventing contaminants from leaving the work zone in case of a breach. The HEPA downflow filter creates a laminar and particle-free ISO Class 3 air cleanliness as per ISO 14644-1 (equivalent to Class 1 as per US Fed Std 209E). inside the isolator to protect the work material inside the main chamber and pass-through.
Air from the work zone and pass-thru is quickly purged out by the fan to keep the area clean. The fan pulls approximately 90% of the purged air back to the plenum and after passing through the HEPA downflow filter again, it is recirculated back to the work one and pass chamber. The high rate of airflow recirculation helps to prolong filter life and reduces the chances of ambient contaminants entering the work zone.
Approximately 30% of the purged air is exhausted through an HEPA-filter to prevent heat build-up inside the isolator that can be detrimental to drug compounding. This exhausted air is replenished by ambient air coming from the top inlet pre-filter and a filter with 80% efficiency for positive pressure model.
Electrical outlets
UV Lamp
IV bars with hooks for handling bags
Exhaust collar*
CCTV and rear view adaptation
Hydraulic Stand Control
Glove Leak Tester
Single- or Multi-piece tray option
Sharps container
Bag In or Bag Out (BIBO)
Bag Welder for Continuous Liner System
*for negative isolator only